JOEST’s new CombiCut 4501.40GbkPrB with its 3D plasma and 3D oxyfuel rotator as well as a fully automatic tool station offers precise bevel cutting, drilling, tapping and countersinking on a work area of 4.5 x 4 m.
On a production area of over 60,000 m², the German company manufactures systems for vibration technology and bulk material processing. In a century of its existence,
JOEST has developed from a Westphalian handicraft workshop into an international company with over 850 employees worldwide. Its core business is the design and manufacture of vibrating equipment, vibrating drives and solutions for the processing of bulk materials. These are manufactured in-house and adapted to customer requirements and local conditions. “The customer gives us a task and we solve it. We manufacture everything in-house and communicate efficiently. We don't sell machines, we sell processes and manufacture solutions to problems, so to speak." This is how Christoph Stief, head of the foreman department at JOEST, describes the custom production process.
“The oxyfuel rotator was one of the decisive factors for us. MicroStep was the only manufacturer who managed to cut our special grate contours with trapezoidal holes and 45° bevels into a 30 mm sheet.”
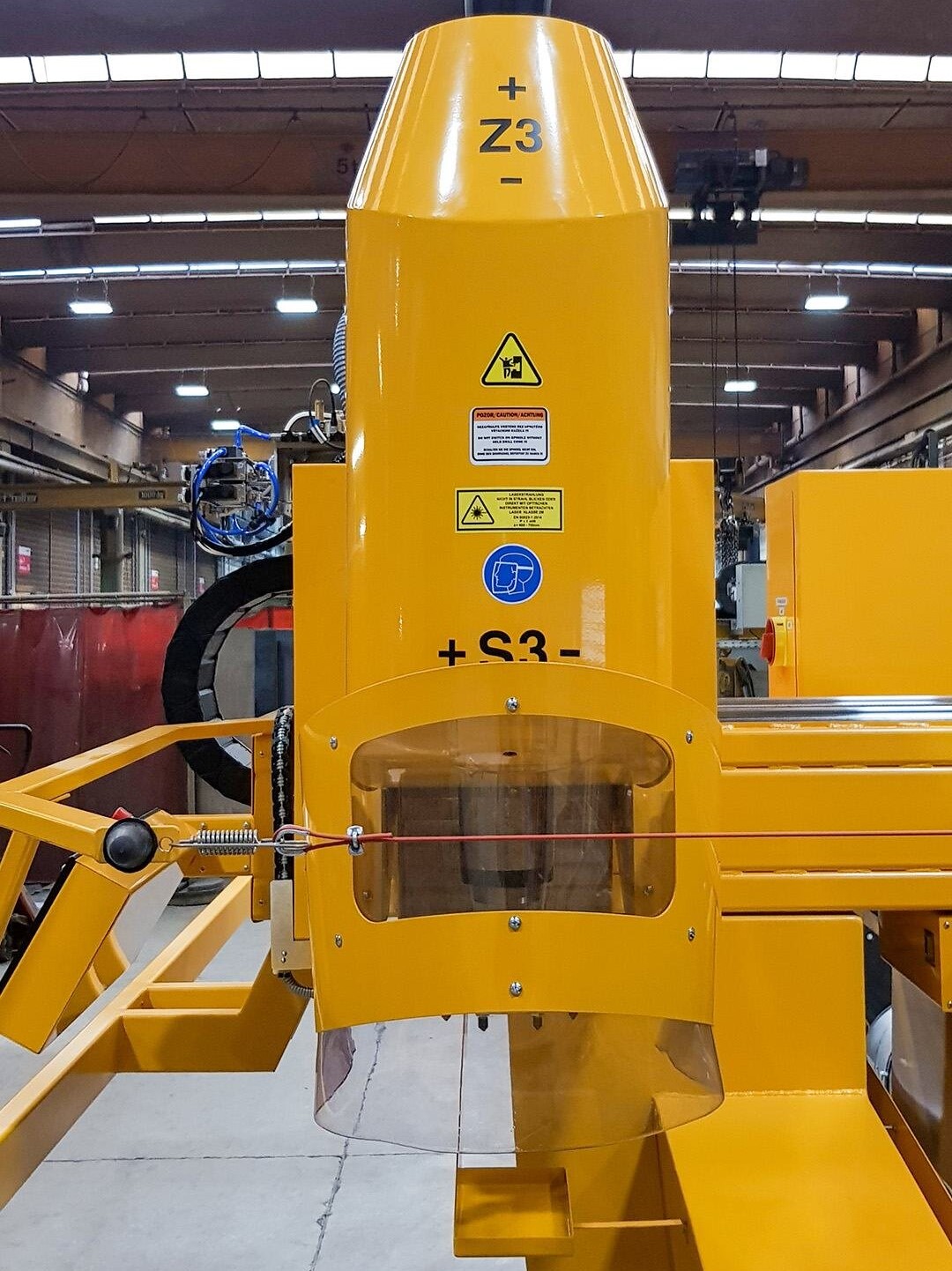 |
Thanks to their fully automatic drilling head and tool magazine, the company can now cut threads in-house. |
The long search For many years, JOEST had been using a 3D plasma and 2D oxy-fuel cutting machine for cutting of construction steel up to 80 mm thick as well as wear-resistant materials such as Hardox. After years of heavy duty use, a new cutting system became necessary to take on the most demanding tasks. In 2016, the company began a long search for a machine that would be able to meet its requirements. Unfortunately, JOEST was left emptyhanded as no suitable system with the required 3D oxyfuel cutting technology was available on the market. Three years later, the company tried again, looking for a multifunctional 3D cutting solution with a drilling system included. After extensive internet research and a comparison of different manufacturers’ solutions, the decision makers in JOEST finally found what they were looking for: MicroStep’s
CombiCut series that could be equipped with both a
3D plasma and a
3D oxyfuel rotator as well as a fully
automatic tool station for drilling, tapping and countersinking. "It's a highly complex machine with a lot of options, really. The oxyfuel rotator was one of the decisive factors for us. MicroStep was the only manufacturer who managed to cut our special grate contours with trapezoidal holes and 45° bevels into a 30 mm sheet,” recalls Mr. Stief.
Many possibilities
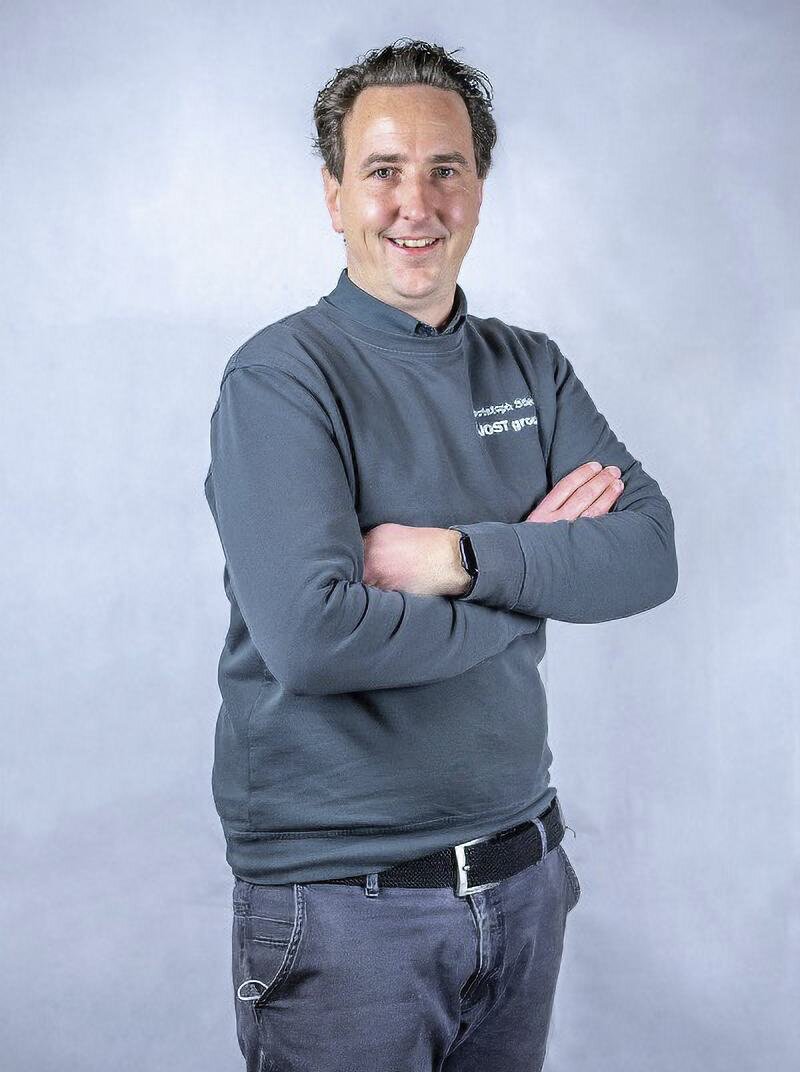 |
"MicroStep´s technology works flawlessly and reliably," says Christoph Stief, head of the foreman department at JOEST. |
The robust and precise CNC machine enables JOEST to run production in two and three shifts.
"MicroStep´s technology works flawlessly and reliably," says Mr. Stief. Thanks to the fully automatic drilling head and tool magazine, the company can now cut threads in-house, "an additional expense that was becoming more and more costly here". JOEST not only uses the plasma bevel head for
weld edge preparation but also to cuts holes in sheet metal 5 – 6 mm thick, saving up to 80 percent of time compared to drilling. With the addition of the oxyfuel bevel head, the company can produce its special components reliably. “Almost all of our parts are unique and the highly complex cutting machine gives us multiple options. We are far from finished improving our production,” says Mr. Stief. An integrated vibrating conveyor in the table automatically removes all the small parts and slag into a designated container. "It was clear to us that we wanted to have this because we were familiar with the topic of 'cleaning' from the old machine," reports Mr. Stief. JOEST is very satisfied with the investment in the multifunctional CombiCut machine and the entire course of the project: "The advice and project planning was simply great."