The integration of oxyfuel technology in MicroStep's rotary bevel heads creates new application areas especially where complex contours with multiple bevel cuts in larger material thicknesses are required. Paired with innovative solutions such as ACTG® and ABP, the new technology proves to be highly efficient and precise.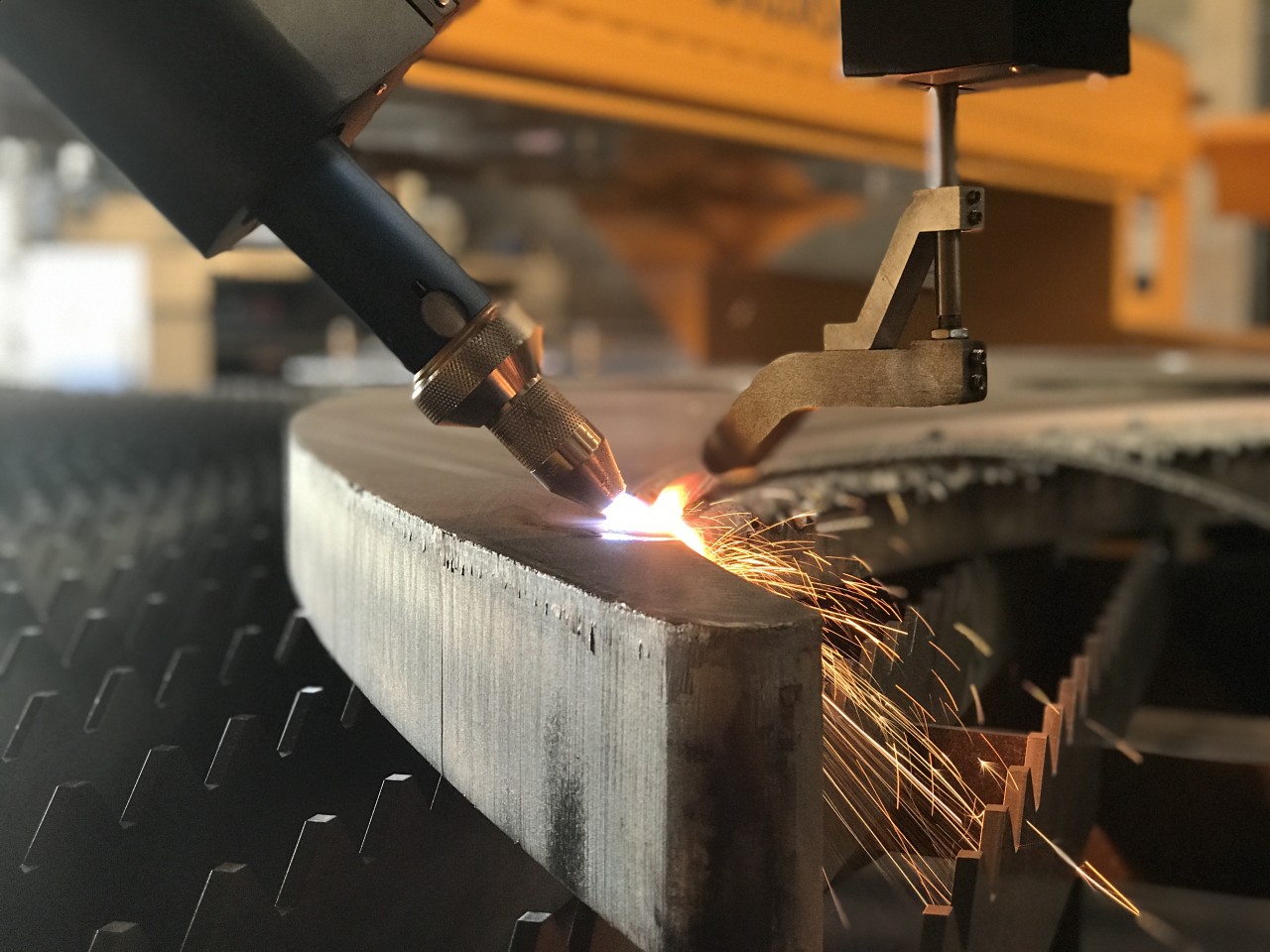
The efficiency of bevel cutting of thick metals is determined by several factors: energy and gas consumption, wear of consumables (cutting nozzles), cutting speed, number of cuts needed to achieve the desired cut profile (for X, Y, K cuts), the possible need for additional material handling between individual cuts and, last but not least, by the volume of waste material that doesn’t belong to the final cut part but also degrades in the cutting process.
The quality of the cut is given by the limitations of the technology itself and, in case of thicker materials, also by its ability to cut through the material of a certain thickness at all. A sustainable production technology needs to be well balanced between these two – efficiency (cost) on one hand and cut quality on the other.
Oxyfuel rotator for weld preparation on thick metals utilizes MicroStep's patented ACTG® technology for automatic compensation of kinematic inaccuracies, and thus delivers reliable cutting results in the long run with a far less frequent maintenance necessary.
Limitations of oxyfuel triple torchesIn today's industrial applications there are commonly cut materials up to a maximum thickness of 50 mm by plasma, utilizing rather high cutting currents 400 – 450 A. In case of bevel cutting, applications from 35 – 40 mm thick tend to be the limit for plasma already: thicker mild steels are traditionally bevel cut by oxyfuel triple torches which allow making two or three cuts at once, creating Y, X or K cut edges in one go. Triple torch technology has certain drawbacks though – the geometry of the torch setup doesn’t allow cutting some types of contours (especially internal beveled edges), the bevel angle is limited to max. 50° and, overall, the maximum material thickness for bevel cuts is usually limited to 80 – 100 mm, making it suitable just for certain applications.
To overcome these limitations, MicroStep came up with an elegant solution: why not integrate an oxyfuel torch into the company's existing rotary bevel head design and enjoy the already developed and established features from plasma also for oxyfuel?
Oxyfuel triple torches make K-cuts in one go but lack the ability to cut really thick (Italy)
Introducing the oxyfuel rotatorThe MicroStep rotator is a 5-axis 3D bevel head with endless rotation and a tilt up to 52° (for plasma torches) that has proven itself in hundreds of installations worldwide. Thanks to the torch pivot point being aligned with its rotary axis, the design is well suited for cutting a great range of bevel shapes including internal contours, variable bevels as well as multiple bevel contours Y, X or K. For oxyfuel, the head has been modified to include an endless gas transmitter, a tactile height measurement system and, most significantly, the torch tilt was increased to 67° which allowed to make use of the generally narrower and pointier oxyfuel torch for cutting material at bigger angles. Compared to triple torch cutting, the advantages are obvious: maximum material thickness for direct beveling increased above 120 mm (depending on application and bevel angle even up to 200 mm), the cut angle increased to a full 0° – 60° range compared to the 20° – 50° range for triple torch. The AC geometry of the bevel head allows to cut significantly smaller radiuses on holes and internal contours, e.g. for thick pipe intersections. Furthermore, oxyfuel rotator with an integrated laser scanner can use Additional Beveling Process (ABP) which greatly expands the possibilities of beveling thick sheets on a cutting machine.
Advantages of additional beveling with oxyfuel – minimum waste, smooth cut surfaces, precise cut contours also for bigger bevel angles, as showcased on the above parts 90 mm thick, Y cut with land size 20 mm, bevel angle 60°, cut with MicroStep ABP technology for a South African customer
Multiple material and gas savings with ABPThe principle of additional beveling is that the part is firstly cut straight, afterwards it is taken out of the sheet, placed on a free spot on the cutting table, scanned for exact contour/position and, subsequently, bevel cuts are added to the contour. For oxyfuel this means that really thick parts (~250 – 300 mm) can be produced with clean bevels with angles ranging up to 60 – 65 degrees – with great saving of gas and material. For Y or K cuts, with ABP the effective bevel cut thickness is significantly smaller compared to direct beveling into a full sheet, which allows to cut bevels much faster and with multiple saving of the cutting gas. Higher cutting speeds also mean that there is a smaller heat-effected zone in the material, i.e. better quality of the final part. The necessary additional part handling times with ABP can be offset by having a machine with multiple straight gas torches, and using ABP on multiple parts in one sequence.
Comparison of direct and additional beveling: Same part with K-type edge profile, cut directly (DBP) into full sheet, produces much more material waste around the part (displayed in pink color), and additionally the effective cut thickness is much bigger which means far greater gas consumption, slower cutting, and bigger heat affected zone around the cut edge. In this case, ABP has clear advantage
Secondly, with ABP there is no additional material waste from the unused part of the bevel cuts because the beveling is done on an already cut contour with no material around it. This presents a significant material saving especially for bigger thicknesses and higher bevel angles. Not to mention that compared to other methods of additional beveling – e.g. using one cutting machine for straight cutting and a separate robot workplace for beveling – the use of one machine for all operations is much more efficient and comes with much lower initial cost. A real case study from Spain has shown that with such a combined MicroStep machine for thick sheet cutting it was possible to achieve time savings in production of up to 85%.
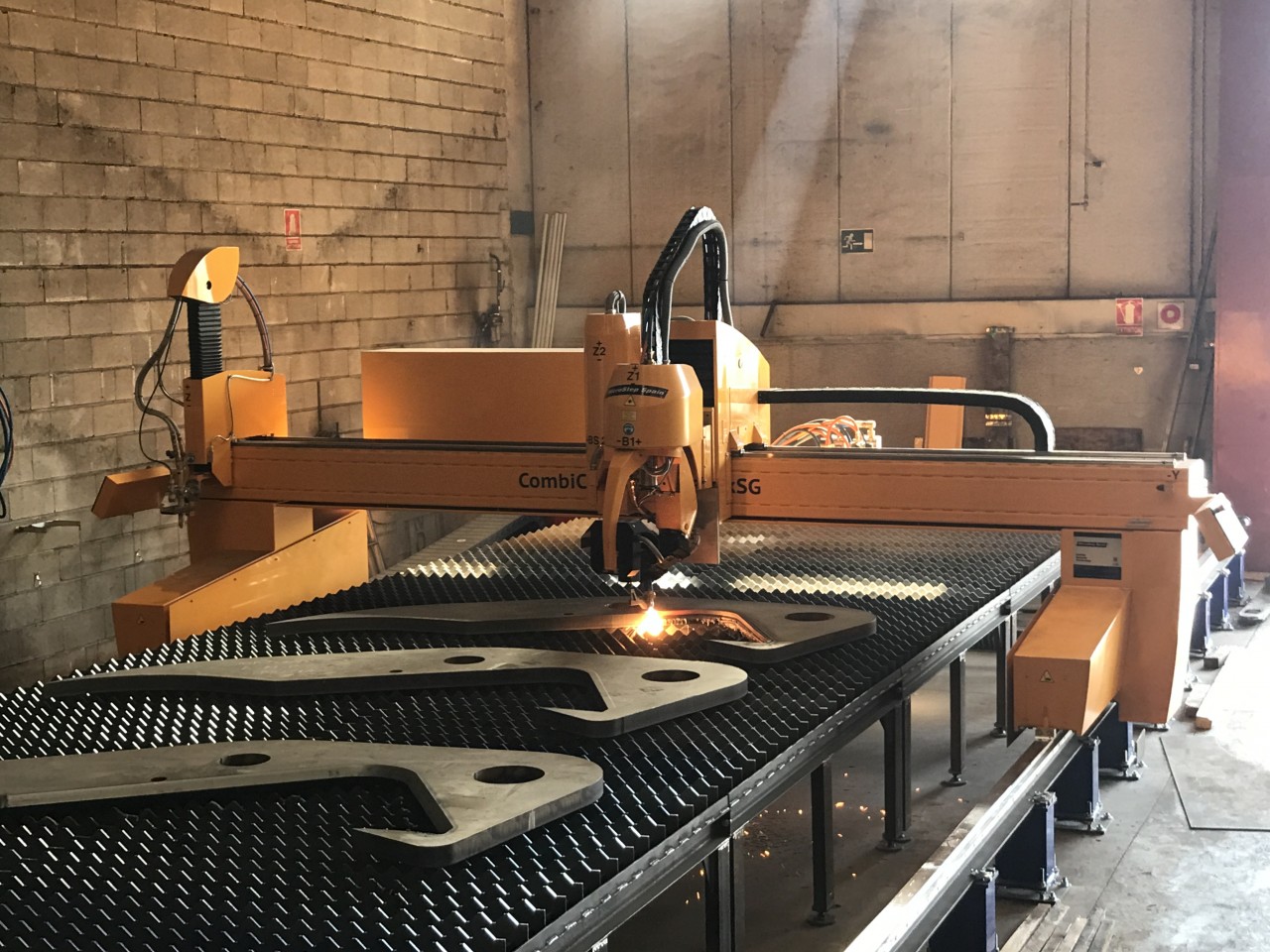
The leading Spanish machine manufacturer Solintal took advantage of MicroStep's oxyfuel rotator and ABP in a big way: the needed steel parts of up to 160 mm thickness with complex bevels on non-linear contours that previously took 6 hours to produce are now ready in 45 minutes.